一、BOG气体处理工艺
处理BOG气体的传统方法有4种:①将储罐内的BOG返回至LNG船舶或LNG槽车,填补卸料时产生的真空;②通过压缩机将BOG压缩至一定压力后,与输出的LNG在相同的压力下直接接触换热,冷凝成LNG送出;③通过压缩机直接将BOG压缩,达到外输管网所需压力后输出;④送火炬燃烧,当BOG量过多而使火炬不能承受时,直接排入大气。
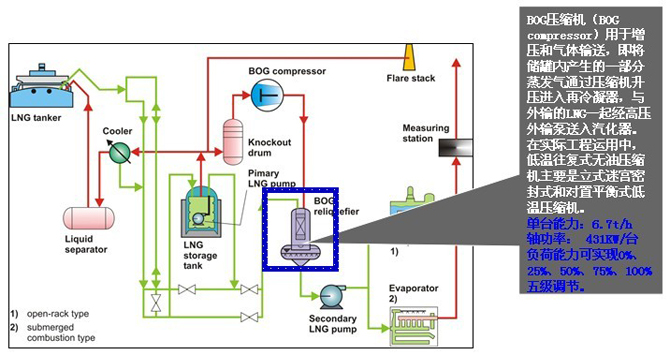
第1种方法虽然过程简单,能量利用最合理,但只有在LNG槽车卸车时才能使用;第4种方法显然最不合理,既不经济也不利于环境保护,只有在紧急情况下才能使用。第2和第3种方法均是将BOG加工再利用,但中间过程有所不同,需根据具体情况,选择不同的工艺。
1.1 直接压缩工艺
直接压缩工艺流程(图1):先将LNG储罐内的BOG通过气液分离罐分离掉液相部分,再将BOG通过压缩机直接压缩到外输管网所需压力后,送入外输管网。
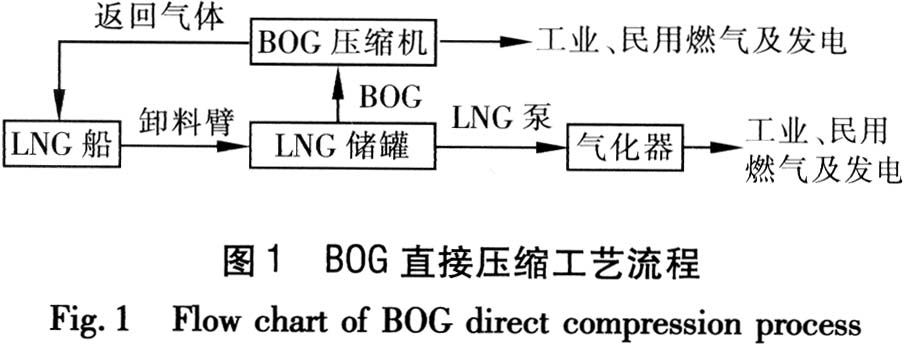
1.2 再冷凝工艺
再冷凝工艺流程(图2):将经气液分离罐分离的BOG通过压缩机加压至一定压力;由储罐内的第一级泵输送出相同压力的LNG,由于LNG经泵加压后的压力大于该温度下LNG的饱和压力,具有一定的“显冷”性;再冷凝器设有比例控制系统,根据BOG的流量控制进入再冷凝器的LNG流量,两者在再冷凝器中直接接触换热;利用LNG的“显冷”将大部分BOG冷凝,确保进入第二级泵的LNG处于过冷态;通过第二级泵加压,经汽化器汽化后送入外输管网。
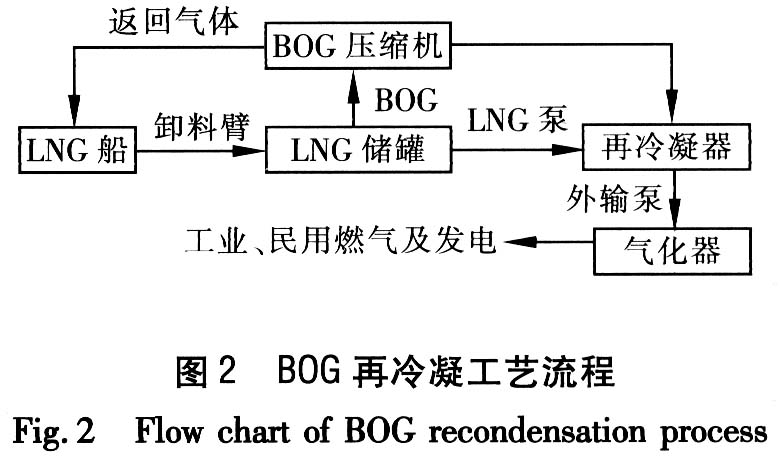
1.3 两种工艺的能耗比较
直接压缩工艺通过压缩机将BOG压缩至管网所需压力,无需再冷凝设备;再冷凝工艺中,压缩机只需承担直接压缩工艺中的一部分工作,剩余工作由LNG高压泵承担。
根据伯努利方程[7],单位质量的流体在输送过程中,从泵或压缩机中所获得的压头可表示为:
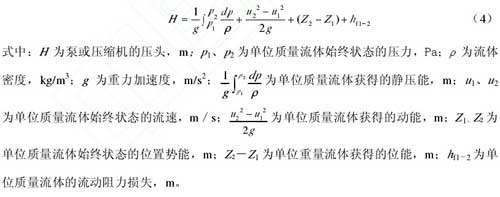
位能与流动阻力损失相比静压能和动能小很多,均可忽略不计。气体相对于液体更容易流动,因此单位质量的气体动能值比液体大,即需要从压缩机获得更多动能。由于同种物质气体密度远远小于液体密度,因此在进出口压力相同的情况下,单位质量气体比单位质量液体获得的静压能大得多。故在相同工况下,泵压缩液体比压缩机压缩气体的能耗小得多,因此,再冷凝工艺能耗更低。
对于大型LNG接收站来说,需要处理的BOG量很大(年接收量为300×104t的大连LNG接收站日平均BOG产生量可达1280t),且储罐储存压力低(LNG大型储罐储存压力接近常压)、外输管网压力高(6~10MPa),采用再冷凝工艺相对于直接压缩工艺处理每千克BOG可以节约0.14kWh的能耗。因此大型LNG接收站利用再冷凝工艺处理BOG显然是比较经济的。
小型LNG卫星站需要处理的BOG量并不多,最多仅3.43t/d;其储罐均是压力容器,工作压力可达0.8~1.0MPa。同时,LNG卫星站离用户较近,外输管网压力较小,国内最大规模LNG卫星站的压力仅有1~1.5MPa,小规模的LNG卫星站压力只有0.3~0.5MPa。这些因素均导致再冷凝工艺的节能效果不明显,处理每千克BOG只能节约0.02kWh能耗,而且小型LNG卫星站无法为BOG的再冷凝提供持续的冷源。因此,对于小型LNG卫星站,使用再冷凝工艺处理BOG节省功耗效果不是很明显,在LNG产业处于起步阶段的背景下,建议使用直接压缩工艺来处理BOG,可以节省再冷凝器设备费用,降低LNG卫星站的初投资。